Page 1 sur 3
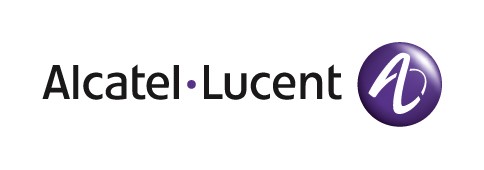
On a un peu tendance à l'oublier mais le réseau Internet est avant tout une histoire de câbles sous-marins. Ces réseaux présents dans la plupart des océans et des mers du globe permettent de relier en haut débit les continents et surtout d'apporter le haut débit dans des territoires isolés ou connecter des pays avec le reste de la planète. Avec l'essor des services, la demande en débit ne cesse de progresser. Il faut alors densifier ces réseaux et poser de nouveaux câbles. Un métier de titan dont Alcatel-Lucent est le leader mondial. Sa
filiale Alcatel-Lucent Submarine Networks (ASN) fabrique et pose des câbles sous marins depuis des décennies. Son usine de Calais existe depuis 1891. D'abord télégraphiques, puis coaxiaux, ces câbles sont désormais en fibre optique. A ce jour, 500 000 kilomètres de réseaux sous-marins ont été déployés par l'équipementier et 50 000 kilomètres par an sortent de l'unité de production.
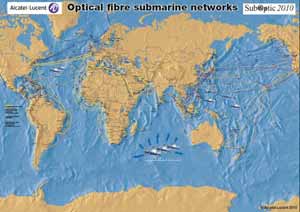
Après une chute de la demande suite à l'explosion de la bulle Internet, la demande repart aujourd'hui à la hausse notamment à travers deux grands nouveaux projets de déploiements qui concernent l'Afrique, nouvel eldorado des opérateurs. Le premier, baptisé WACS (West Africa Cable System) reliera l'Afrique du Sud au Portugal (14 500 kilomètres). Il sera achevé en 2011 et renforcera la connectivité des pays tout au long de son parcours (capacité de transmission : 10 Gb/s). Montant du projet : 600 millions de dollars. Le second, ACE, qui implique une dizaine d'opérateurs africains avec une forte présence d'Orange doit également améliorer la couverture en Afrique de l'Ouest.
Avec ces deux câbles, tous le continent africain devrait être couvert en Internet haut débit d'ici 2012 avec une capacité globale de 16,6 Tb/s contre 0,2 aujourd'hui. On imagine l'attente des populations... 76 points de raccordements à terre seront déployés contre 16 aujourd'hui. Car certains pays attendent la connexion sous-marine avant de commencer à déployer le réseau terrestre. Alcatel-Lucent a en charge la fabrication et la pose de ces câbles grâce à ces bateaux câbliers. L'occasion pour nous de visiter son usine de Calais (400 salariés) et son bateau câblier, l'Ile-de-Bréhat.
Avec ces deux câbles, tous le continent africain devrait être couvert en Internet haut débit d'ici 2012 avec une capacité globale de 16,6 Tb/s contre 0,2 aujourd'hui. On imagine l'attente des populations... 76 points de raccordements à terre seront déployés contre 16 aujourd'hui. Car certains pays attendent la connexion sous-marine avant de commencer à déployer le réseau terrestre. Alcatel-Lucent a en charge la fabrication et la pose de ces câbles grâce à ces bateaux câbliers. L'occasion pour nous de visiter son usine de Calais (400 salariés) et son bateau câblier, l'Ile-de-Bréhat.
La lente genèse d'un câble sous-marin
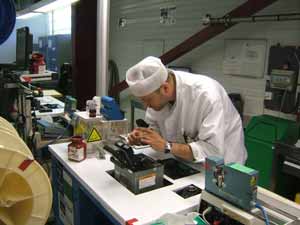
La fabrication d'un câble sous-marin exige une expertise particulière. Plongés à 8000 mètres de profondeur, ils doivent résister aux assauts du sel marin mais surtout à la pression. Surtout, leur longueur exceptionnelle (en moyenne 6000 kilomètres entre deux extrémités contre 1000 pour les câbles terrestres) impose des spécificités particulières. Si la fibre est la même, les techniques de protection (gainage, blindage, enrobage...) sont nettement plus importantes et complexes. Alcatel-Lucent reçoit d'abord la fibre optique à l'état brut. Chaque câble sous marin comporte 4 fibres (d'une taille de 250 microns et d'une longueur d'environ 20 kilomètres). La première étape consiste à effectuer des soudures pour obtenir des segments de 70 kilomètres (!), la longueur moyenne d'un câble sous-marin.
Le travail est effectué par un technicien assisté d'une machine à souder qui effectuer l'alignement au laser. Cette soudure est beaucoup plus précise que dans le domaine de la fibre terrestre afin d'obtenir une fibre moins atténuante. Des tests de traction sont ensuite effectués, ils sont redoutables car le câble sera soumis lors de la pose à des pressions latérales très importantes.
Le travail est effectué par un technicien assisté d'une machine à souder qui effectuer l'alignement au laser. Cette soudure est beaucoup plus précise que dans le domaine de la fibre terrestre afin d'obtenir une fibre moins atténuante. Des tests de traction sont ensuite effectués, ils sont redoutables car le câble sera soumis lors de la pose à des pressions latérales très importantes.
Seconde étape : la coloration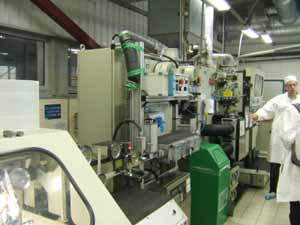
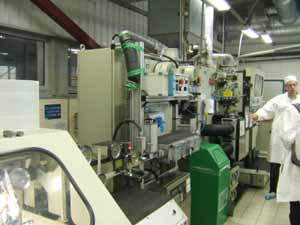
Les fibres passent dans des machines spéciales pour être colorées. Objectif : permettre de les identifier facilement surtout en cas de casse. Ce qui n'est pas rare : les tremblements de terre sous marins provoquent régulièrement des dégâts. Il s'agit également de les protéger de la poussière, ennemie numéro un de ces composants.
Fabrication des protections
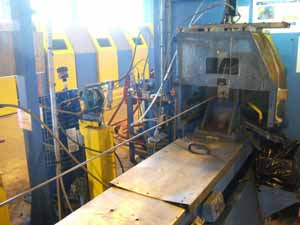